The Function of Foam Control in Enhancing Item Top Quality and Performance
Foam control is an often-overlooked yet essential component in the search of product high quality and operational performance throughout varied industries. This conversation will discover the complex influence of foam on both item integrity and production procedures, raising essential questions about the approaches that can be used to optimize foam control.
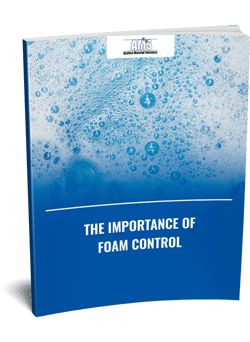
Comprehending Foam Development
Foam formation is an intricate sensation that can significantly impact product top quality and functional effectiveness across different sectors. It occurs when gas bubbles become trapped in a liquid, bring about the development of a frothy structure. Several elements add to this process, including the chemical and physical buildings of the liquid, the presence of surfactants, and the problems under which mixing happens. Recognizing these variables is essential for managing foam properly.
The liquid's viscosity and surface area tension play essential duties in foam stability. Surfactants, as an example, can minimize surface area tension, advertising bubble development yet also boosting foam security, which can be troublesome in certain applications. Mechanical frustration, temperature changes, and the presence of contaminations can exacerbate foam generation, making it vital to monitor these facets during production processes.
Industries such as food and drink, pharmaceuticals, and chemical manufacturing must be especially cautious concerning foam control. By realizing the hidden systems of foam formation, organizations can carry out targeted approaches to reduce its impacts, thus protecting operational efficiency and making certain regular item performance.
Impact on Product Top Quality
The presence of foam can substantially compromise item top quality across numerous industries. In making procedures such as food and drink, pharmaceuticals, and cosmetics, extreme foam can bring about irregular product formulations. As an example, in food manufacturing, foam might catch air, impacting structure and taste, which can inevitably change consumer understanding and contentment.
Additionally, foam can prevent the harmony of paints and finishes, resulting in flaws like bubbles and unequal surfaces. In pharmaceutical applications, foam can conflict with the precise application of fluid medications, possibly affecting therapeutic efficacy and individual security. These top quality problems not only decrease the end product's charm but can additionally result in expensive recalls and damages to brand credibility.
In addition, the existence of foam can make complex top quality control procedures, making it hard to accomplish precise dimensions and regular outcomes. Effective foam control not only alleviates these risks yet also improves total product top quality by ensuring that formulations meet strict market criteria. By buying foam control approaches, firms can safeguard their products, boost client fulfillment, and preserve an one-upmanship in the market.
Operational Difficulties From Foam
Reliable operations in various sectors can be badly interfered with by the visibility of foam, which positions numerous obstacles throughout production procedures. Foam can impede mixing and reaction times, hindering the performance of chemical processes. In markets such as food and beverage, foam formation can bring about inaccurate fill degrees, leading to item waste and inconsistencies in product packaging.
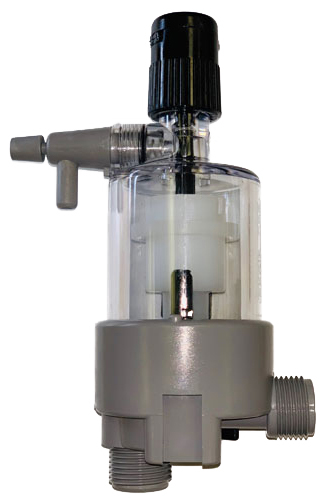
In settings where hygiene is paramount, such as pharmaceuticals and food handling, foam can make complex cleaning methods, producing hidden tanks for pollutants. This not just elevates high quality problems but likewise can result in compliance issues with governing requirements.
Additionally, the mental basics influence on drivers can not be ignored; excessive foam can create a chaotic workplace, causing decreased morale and productivity. In recap, dealing with the functional obstacles postured by foam is vital to preserving effectiveness and product quality in various sectors.
Strategies for Efficient Foam Control
How can industries successfully minimize the obstacles posed by foam? Effective foam control techniques are vital for enhancing product quality and operational performance. One main method is the usage of defoamers, which are chemical agents designed to minimize or remove foam development. Selecting the proper defoamer needs a comprehensive understanding of the specific process conditions and the products entailed.
Along with chemical solutions, process optimization plays a vital role in foam management. Industries can evaluate and change these details criteria such as mixing temperature level, pressure, and speed to decrease foam generation. Executing tools modifications, like setting up foam-breaking tools or adjusting tank layout, can further help in reducing foam levels.
Regular monitoring and evaluation of foam behavior within production processes are also essential. Making use of sophisticated sensing units and analytics can provide real-time information, permitting prompt interventions and changes. Team training is equally essential; making sure that workers are experienced concerning foam characteristics and control techniques can bring about aggressive foam monitoring.
Study and Market Applications
While many industries encounter unique obstacles associated with foam control, situation studies reveal that customized approaches can significantly boost both product quality and functional efficiency. In the pharmaceutical sector, as an example, a leading producer carried out a customized foam control strategy that lowered foam formation throughout fermentation procedures. This innovation not just improved return by 15% but also lessened contamination risks, guaranteeing greater product stability.
Similarly, in the food and beverage market, a significant milk manufacturer challenged extreme foam during pasteurization - Foam Control. By presenting a specialized antifoam agent, they decreased handling time by 20%, which straight converted to enhanced throughput click this link and decreased energy consumption. The application of foam control gauges ensured regular item texture and preference, enhancing brand name loyalty
In the chemical production industry, a study highlighted the successful application of foam control in wastewater therapy procedures. The execution of a real-time monitoring system enabled drivers to adjust antifoam dosage dynamically, resulting in a 30% decrease in chemical usage and enhanced effluent high quality.
These study show the varied applications of foam control throughout markets, stressing its vital function in improving product quality and functional effectiveness.
Final Thought
In verdict, reliable foam control is integral to improving product high quality and operational performance across various industries. Inevitably, prioritizing foam control contributes to boosted efficiency, safeguarding brand name credibility, and boosting client contentment, highlighting its significance in high quality guarantee within making procedures.
Foam control is an often-overlooked yet essential component in the search of item top quality and functional efficiency throughout diverse industries. Staff training is equally important; making sure that employees are knowledgeable about foam dynamics and control methods can lead to positive foam monitoring.
While many industries encounter special difficulties associated to foam control, case studies disclose that customized strategies can significantly enhance both product top quality and operational effectiveness (Foam Control). In the pharmaceutical industry, for circumstances, a leading supplier executed a custom foam control technique that decreased foam development during fermentation processes.In verdict, effective foam control is important to enhancing product top quality and functional performance throughout different sectors